China+1: Why German Industry Must Diversify Now to Secure Its Supply Chains
Germany’s industrial machine still leans heavily on China. But growing risk factors—from trade tensions to geopolitical instability—are pushing companies to rethink their sourcing strategies. “China+1” is no longer a theory. It’s the new playbook. Here’s why it matters now—and how to get it right.
The Need for Diversification: How German Companies Can Secure Their Supply Chains
China remains the most critical import partner for German companies, but the risks of this dependency are becoming increasingly apparent. As a result, the “China+1” strategy – an approach which sees companies reducing their reliance on Chinese suppliers by adding at least one more sourcing country to the mix - is gaining traction as a key lever for long-term supply chain resilience. Companies should diversify sourcing to include India and ASEAN countries - an area where H&Z can offer immediate support.
The Dependency Problem
Between 2015 and 2023, German imports rose by more than 40%. Meanwhile, German companies remained heavily reliant on Chinese suppliers. China is still Germany’s most important import partner, accounting for 10.9% of all imports—roughly €160 billion annually. This dependency is particularly stark in the manufacturing sector, where electronic and electromechanical components originate predominantly from China. In key product categories such as passive components, printed circuit boards, and cable harnesses, imports from China outnumber those from other Asian countries by a factor of five.
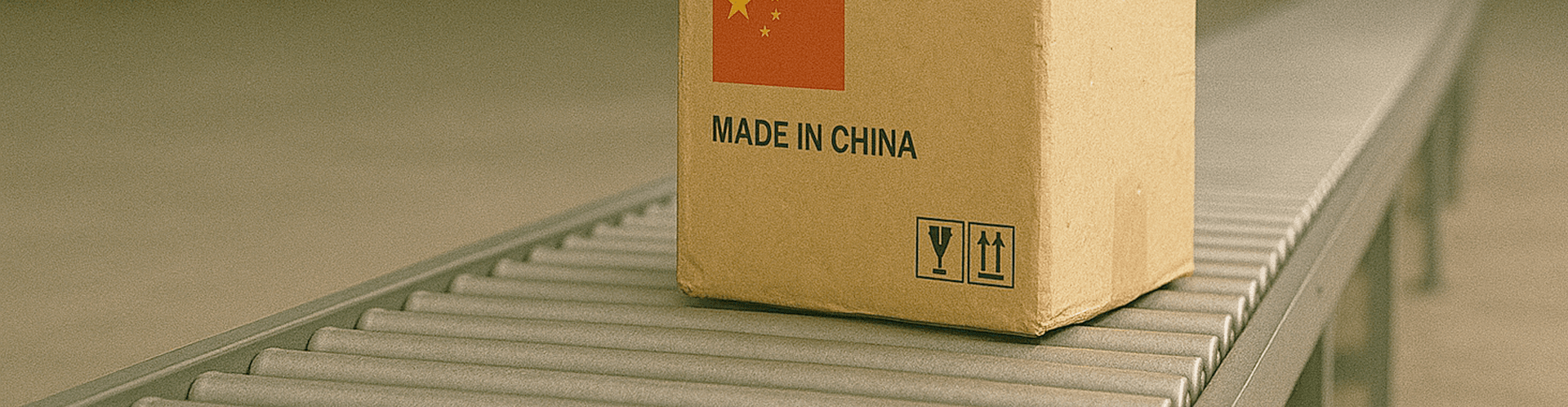
While this is nothing new, recent shifts are making the risk impossible to ignore. Facing internal economic challenges, the Chinese government is ramping up subsidies and export incentives to bolster its manufacturing sector. This state-driven export push is fuelling international countermeasures in the form of punitive tariffs which are increasing costs. In addition, geopolitical tensions are adding a layer of uncertainty: China's increasingly assertive posture toward Taiwan is fuelling fears of conflict that could severely disrupt production and global supply chains.
For procurement leaders, the impact of these recent changes is clear: rising landed costs, delayed deliveries and growing uncertainty – all highlighting the urgent need to diversify risk. This comes in the form of the “China +1” approach. While German companies have been exploring this approach since the early 2000s, it has now evolved from a cautious option to a strategic imperative.
So, Who’s Your +1?
India and Southeast Asian nations are increasingly emerging as viable alternatives to China. Between 2005 and 2023, imports of key industrial goods from ASEAN countries rose by 200%, according to OEC data. India, too, has recorded steady double-digit growth in recent years, albeit from a lower base.
A closer look reveals particularly strong momentum in Malaysia and Thailand across all product groups relevant for industrial goods companies. Between 2015 and 2023, imports from Malaysia in grew by 284%, and from Thailand by 211%. In comparison, imports from China in the same period rose by just 86%.
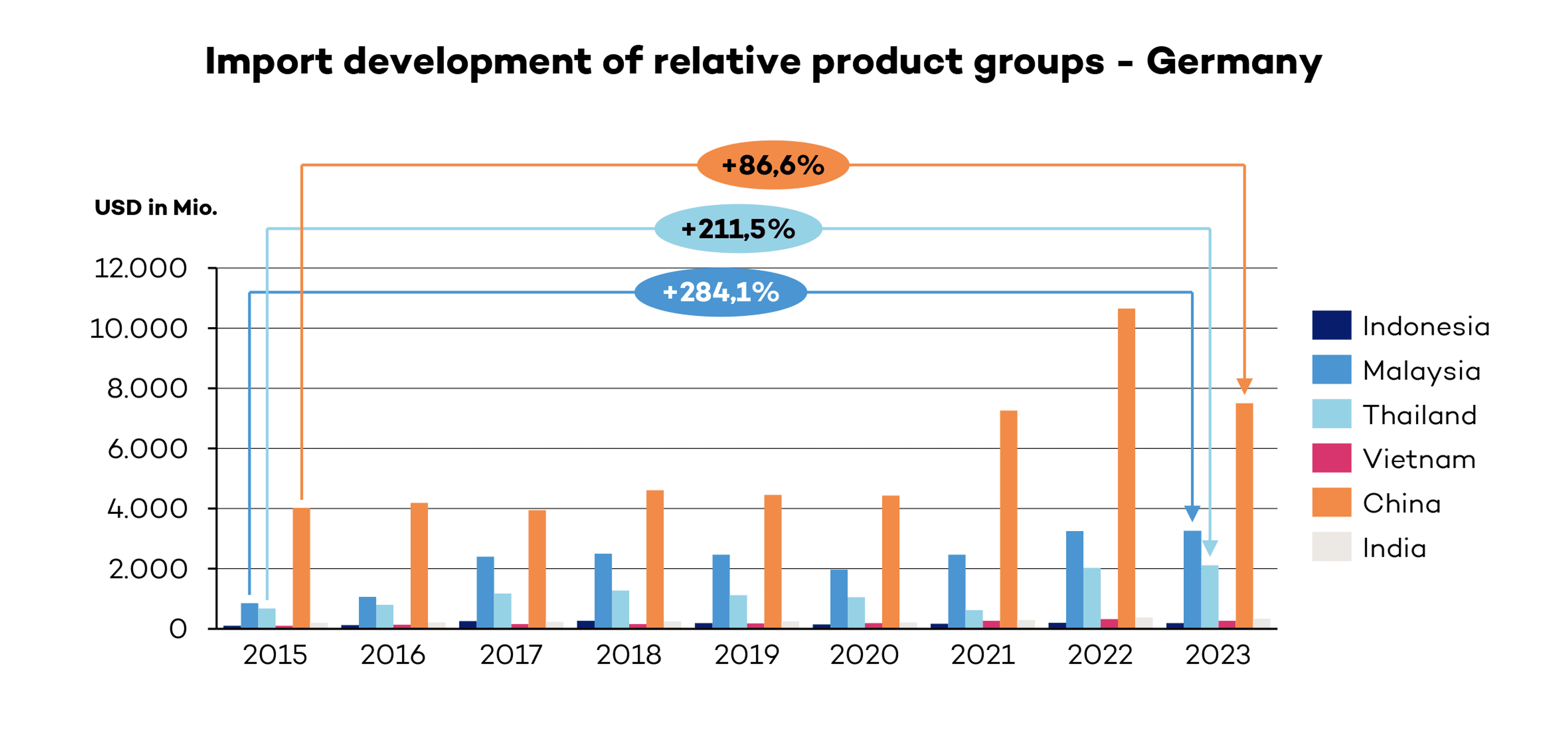
Import trends for printed circuit boards offer a glimpse of an emerging shift. While China remains a key supplier, countries like Thailand and Vietnam are becoming increasingly important sourcing markets. Between 2015 and 2023, Germany's imports of printed circuit boards increased by 24% from Thailand (rising from USD 68mn to 85mn) and surged by 655% from Vietnam (from just USD 431k to 3.2mn). Other product groups, especially in the electronics and electromechanics sectors, are likely to follow this trend. This clearly demonstrates the potential to diversify supply chains and successfully shift sourcing away from China.
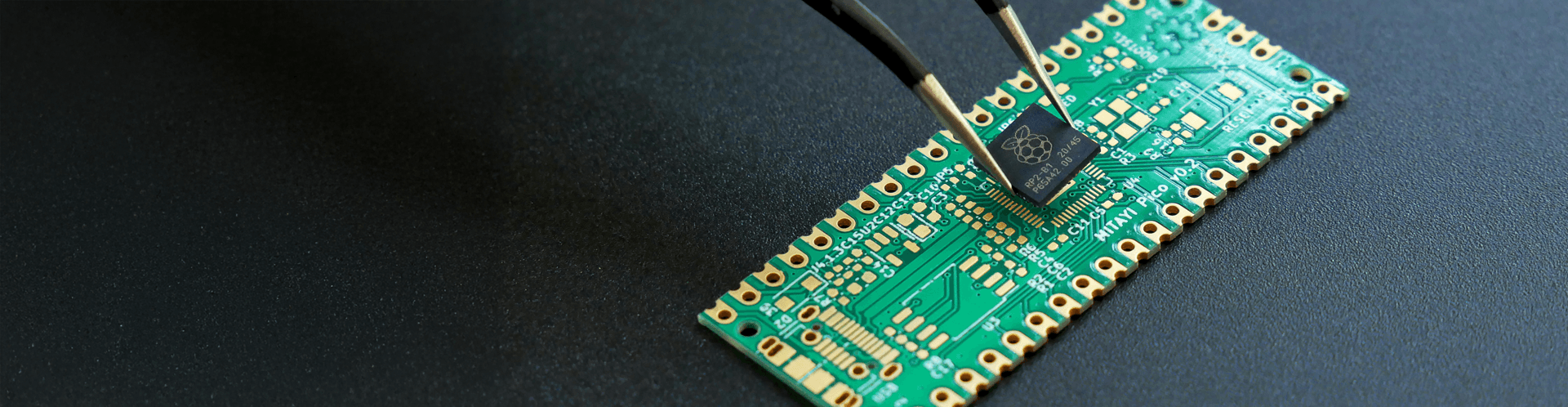
H&Z Approach: Turning Strategy into Action
At H&Z, we support procurement leaders in translating “China+1” from concept to concrete results. Our approach combines strategic insight with hands-on implementation:
- Proactively identify risks across global and regional supply chains, uncover opportunities for mitigation and define a clear, actionable plan.
- Strengthen relationships with resilient, globally active suppliers - those with multi-country manufacturing footprints - and support the relocation or expansion of production facilities outside China.
- Diversify the supplier base to create regional and product-level flexibility, optimising landed costs and reducing the risk of supply disruptions through smarter sourcing strategies.
Let’s move beyond dependency, diversify and build resilient supply chains for the future.
You might be also interested in:
Your search result is empty. Try another filter combination.